Aalten, March 2021: After Dibella gave the starting signal for the "Dibella up" circular-flow concept in August 2020, thousands of high-quality bags have already been made from used hotel textiles. Now the company is presenting another upcycling project: As part of a feasibility study, organic Fairtrade napkins that could no longer be rented out by the company were turned into jeans.
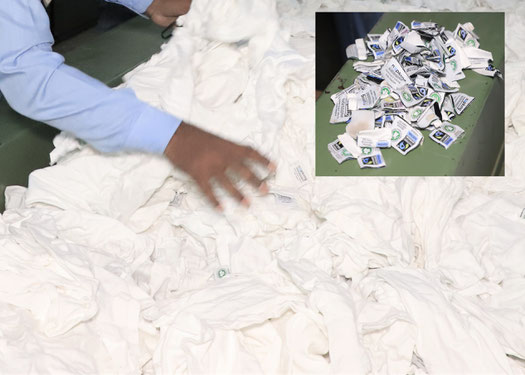
With a far-reaching upcycling project, Dibella has been committed to the reuse of raw materials bound in hotel textiles since August 2020. The company has developed various concepts for this and the first project was already a hit: bed linen that can no longer be rented out from the Lamme Textile Management (Nederhorst den Berg) operations is being processed into tens of thousands of high-quality bags for the Scandinavian market. The second "Dibella up" project also promises successful recycling of used object textiles. Within the framework of a feasibility study, almost 5,000 discarded napkins were used for jeans production in Pakistan. The special feature of the process is the traceability of the raw materials through all processing stages.
Origin: Known
The napkins made of pure organic Fairtrade cotton originated in India. There, the fibres were grown and harvested by micro-farmers of the Chetna cooperative and then processed into durable textiles by a certified company. From Dibella, the napkins went to Lamme Textile Management, where they went through the use process in laundry and catering for many years. All stages were traceable by means of a "Respect Code" with which each piece was marked.
"The origin of our fibres plays an important role in upcycling, because a transparent supply chain does not end with the reuse process. It continues there," explains Ralf Hellmann, Managing Director of Dibella.
Back to the origins
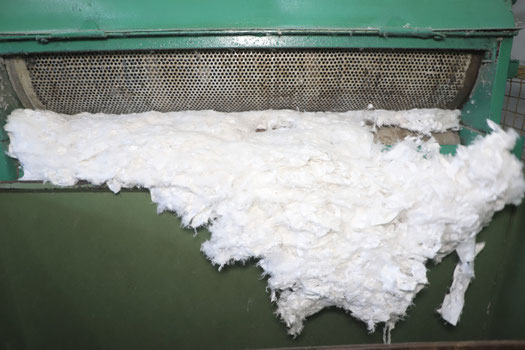
In the recycling project, the original supply chain was reversed: Dibella transported the organic Fairtrade napkins discarded by Lamme Textile Management to Pakistan. There, the goods were shredded and the organic Fairtrade cotton fibres recovered in a full-scale textile plant specialising in sustainability. In the next step, they were mixed with "fresh fibres", spun into yarns for denim production, woven, finished with sustainable processes, subjected to quality tests and then made up into jeans.
Benefit for the environment
"With the feasibility study, we have found a way for the sensible reuse of a high-quality natural raw material and the resources tied to it. This enables us to further reduce the ecological impact of our cotton range and to continue the recycling concept into the next product generation: After use (as a napkin) is before use (as jeans)," says Ralf Hellmann happily.