The laundry industry will see further automation. Robotics and artificial intelligence (AI) will continue to produce new solutions that can run 24/7 and at the same time alleviate the labour shortage. At the same time, the automated systems place the highest quality demands on the textiles.
Preparing textiles involves a lot of manual labour, which is why the profession of textile cleaner is even classified as a skilled trade in Germany. Even in industrial laundries, where various processes are already automated, nothing works without people: they sort soiled laundry, fill washer extractors, operate ironers and towel folding machines, pack stacked laundry or commission upcoming tours. However, the companies are facing a growing problem. There is a shortage of staff - and this is unlikely to change in the coming years.
The challenge of labour shortages can only be solved by further automating processes. At the end of this process, we may see a largely automated laundry. However, it could be some time before this happens. However, there are already the first systems that use AI and robotics to take over manual labour.
One of the latest developments deals with the separation and feeding of terry towels to the folding machine. Instead of an employee taking the laundry out of the laundry trolley, spreading it out and feeding it into the folding machine without creases, robots take over the task.
The process is similar to the fully automated assembly of a car. The feat is achieved by utilising state-of-the-art technology and AI. With the help of image recognition systems, a mechanical arm grabs a towel from a laundry trolley. Thanks to cameras and sensors, the robot recognises the corners of the towel and places it on a conveyor belt so that another robot arm can pick it up and clamp it in two grippers. These then spread out the width of the towelling and place it on the conveyor belt of the folding machine. The rest is familiar: The textile is folded, stacked and, if necessary, packaged. According to the company, towels can be processed in a range of sizes from 30 x 30 to 100 x 200 cm and - thanks to AI - without restrictions in terms of colours and shapes. The system will soon even be available with stain and hole recognition as well as logo alignment for customers' own towels.
However, there is still some way to go before fully automated separation, quality control and finalisation of the textiles: according to the manufacturer, the robots can process mixed batches with cloths of different sizes, but in practice the diversity of the textiles is proving to be a bottleneck.
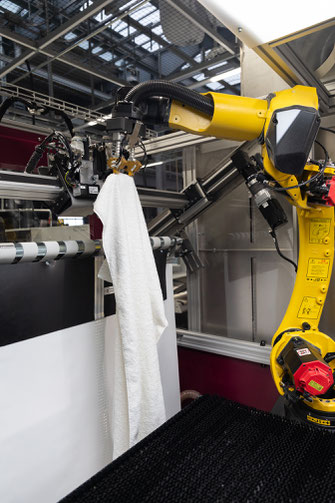
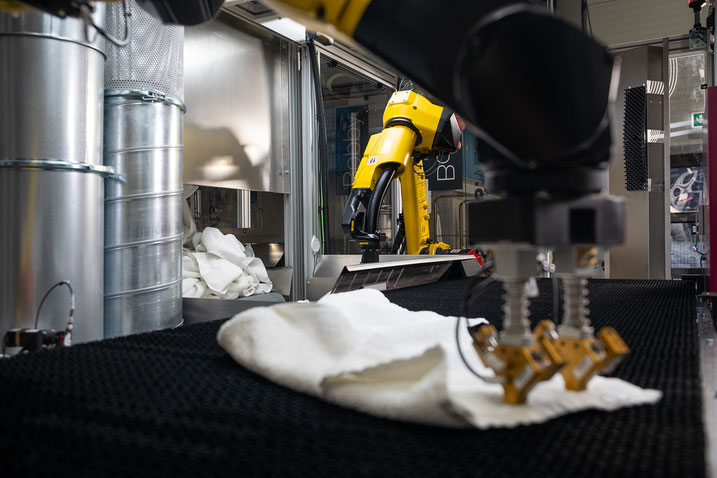
Another system that facilitates preparatory work on the clean side of a laundry is used to separate large items before the ironer. The corresponding system is equipped with pick-ups into which sheets - which can be fed from a sack, a conveyor belt or a laundry trolley - are clamped. They then spread the sheets out to their full width and lift them upwards, whereby they are measured on the one hand and "shaken out" on the other. The piece of laundry is then transferred to the ironer, plain and sorted. This makes handling large items of laundry much easier. However, it is still not possible without staff: each item must be manually fed into the pick-up clamps by employees.
Intelligent systems not only replace manual activities in a laundry, but can also take over quality control. With the help of image recognition systems and AI, clean bed linen can be checked for defects on the wrong side and towelling can be checked for defects in front of the folding machine. To do this, the entire width of the product is scanned. The features that cameras can identify include colours, lines, logos, sizes and shapes as well as defects such as holes, tears and stains. Depending on the configuration of the system, it is also possible to automatically sort the laundry based on predefined characteristics so that at the end of the process, unmixed stacks are output onto a conveyor belt. As practical as the automatic control is, it is also "stupid" to set up. The system has to painstakingly "learn" which defects are considered faults and which are tolerated. This is not easy: time and again, laundry items are recognised as no longer acceptable, even though experienced employees would classify them as acceptable. So even at these workstations, it is not possible without people.
The use of robot technology began on the clean side of a laundry. In the meantime, it has also been possible to automate the sorting of dirty laundry.
To do this, a robot arm first separates the items fed on a conveyor belt and then feeds them to an image recognition system that scans the items. The downstream AI identifies the item and forwards the data to the "corresponding" discharge chute. This opens as soon as the item of clothing, a terry towel or a bed sheet arrives and drops it into a laundry bag or roll container. If the laundry is already equipped with transponders, sorting can also be controlled using RFID technology. It is also possible to sort the dirty laundry into different washing batches based on colour - for example into light and dark. However, the colour criterion has a catch: hotel textiles have a closely spaced colour palette, which makes it difficult to clearly separate the individual shades - especially after repeated washing. It is therefore conceivable that coloured and pure white goods are washed together, although they are actually assigned to two different processing programmes.
The course has been set for increasing automation in the laundry industry. However, the systems are "sensitive". As the systems are equipped with numerous cameras, they cannot tolerate excessive lint formation.
But even if plant manufacturers equip their visualisation systems with automatic calibration and time-controlled cleaning functions, the smooth running of the processes depends on the textiles: They must be optimally matched to the requirements of industrial laundry care and fulfil particularly high quality criteria. And it is precisely these requirements that Dibella's hotel textiles have always fulfilled.
- We use high-quality ring or AirJet yarns for our textiles. They bind the fibres particularly tightly into the yarn composite and prevent their unwanted release and the associated lint formation. As a result, camera systems and other sensitive components are better protected against fibre dust deposits. However, it is not possible without careful handling of our qualities in a factory: if bed sheets, terry towels and the like are overdried, the cotton is irrevocably damaged and the fibres break. In subsequent processes, these fibres are then released from the textile composite, accumulate in the water cycle or contribute to the formation of fluff in a production hall.
- Our bed and table linen is designed to be particularly stable and durable in the face of mechanical forces (e.g. in the washing, dewatering and drying process). Even after countless washes, our qualities have good strength values and guarantee smooth processes even in robot-controlled laundry separation and spreading.
- The cotton contained in our qualities is a natural fibre that shrinks during washing. We have set shrinkage limits for all our textiles. This means that our customers can be sure that the fabric remains true to size and that the pre-set parameters on a spreading robot or folding machine are adhered to.
- The gripper arms of a robot on an automatic terry towelling folding machine are trained to grip the corners or edges of a towel. Therefore, it is not just a matter of high edge strength. The labels are also firmly sewn so that they hold even if the robot arm has grabbed them incorrectly and the entire weight is on them.
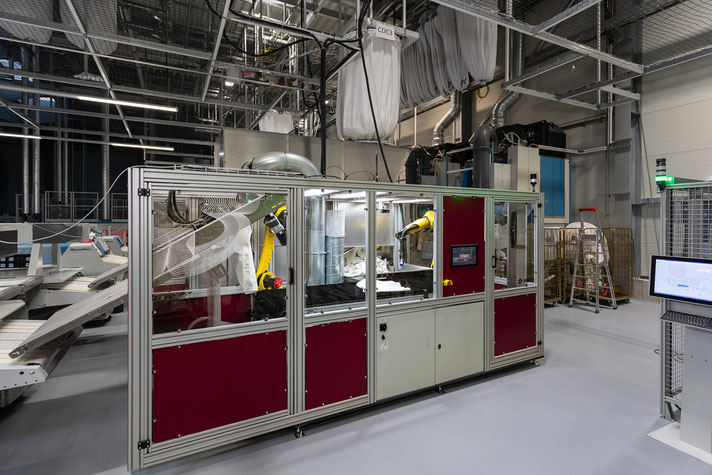
- Colour fastness plays a key role in automatic sorting processes. Cameras must detect the colour tone and convert it into commands for further processing. The AI is "fed" with tolerance values for the correct allocation of the coloured goods. However, these are relatively low for closely matched colours such as champagne and ivory. For intelligent colour recognition to work, a high level of colour stability must therefore be maintained even after many cycles, which is also essential for pool goods. We therefore only dye our coloured qualities with dyes that are resistant to light, chlorine and boil-washing. When treated properly, they guarantee a consistent spectrum and therefore also facilitate camera-based quality control and sorting.
- RFID technology is gradually gaining ground in textile services. Each item of laundry fitted with a transponder carries important information, can be controlled through the process and can be localised. The technology also simplifies the automation of a laundry because the criteria for the individual processing steps can be stored. Dibella textiles can be fitted with different transponders. We sew the transponder types requested by the customer inconspicuously into the hem edges. On the one hand, this ensures a smooth process flow in the laundry, while on the other, the "data carriers" remain invisible to the hotel guest.
The increasing development of artificial intelligence will also lead to further automation of processes and quality assurance in textile services. For example, it is conceivable that an item of laundry could be scanned regularly for its material composition and removed from the cycle if the fibre content falls below a minimum level. Cameras could detect the pilling content of a textile and decide whether it should remain in or be removed from the cycle. Whatever possibilities AI may bring in the future, two things will be particularly important: very close cooperation between the textile supplier and the textile service company and high product quality. We at Dibella are valued by our customers for both.
Supplier of automation solutions in the flat laundry sector:
- Sewts.de
- Laundry-robotics.com
- Jensen-Group/viking
- Mobics AIScan
- Inwatec.dk
- Kannegießer/Quantex
All photos by sewts.de